Hot Off the Presses: How 3D Printing Could Help Construction Go Green
3D printing has the potential to upend the cement industry and, if used correctly, reduce the carbon footprint of the construction process, according to a new paper from Georgetown researchers published in Communications Engineering.
The cement industry, which accounts for about 8% of global carbon dioxide emissions, is both notoriously carbon intensive and inextricably tied to future population growth and development. Concrete and cement are also some of the most used resources in the world, second only to water in terms of consumption, the researchers noted.
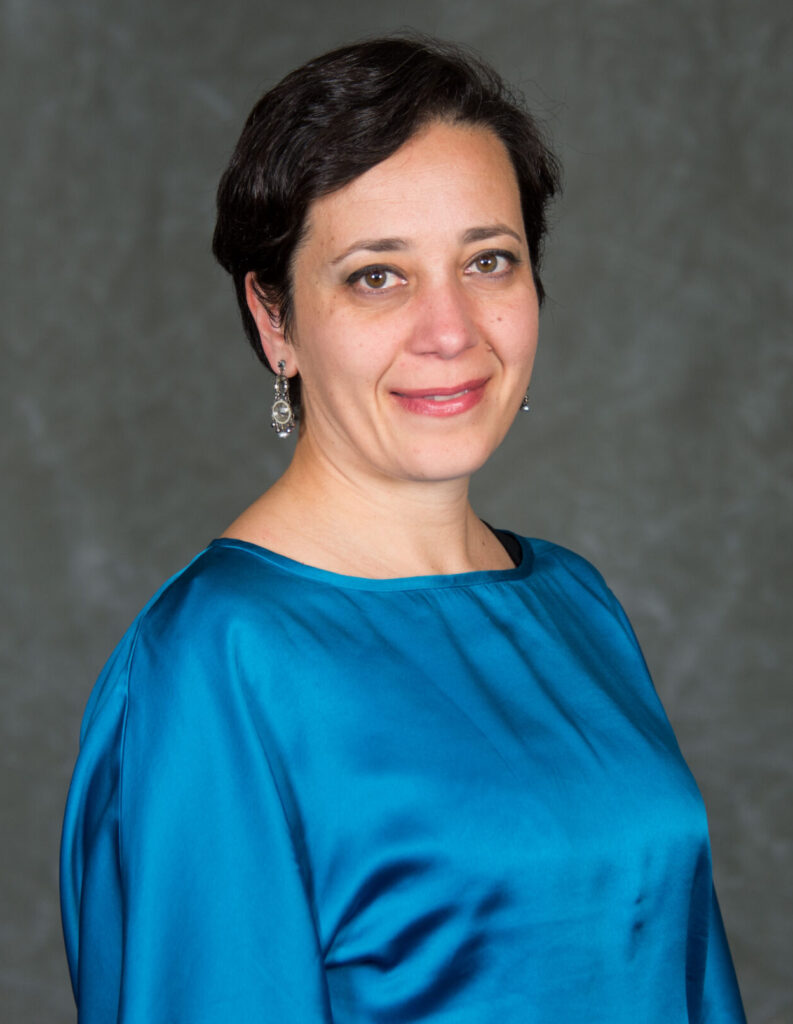
Emanuela Del Gado, director of the Institute for Soft Matter Synthesis and Metrology.
In their joint paper, Emanuela Del Gado, a professor in the Department of Physics, and Joanna Lewis, a Distinguished Associate Professor of Energy and Environment, argue that reducing the cement industry’s impact on the environment will not only help the U.S. meet its goals under the Paris Agreement but will also empower construction companies around the world to use greener products.
Cleaner Structures, Cleaner Mixtures
3D printing uses computers to build three-dimensional structures through an additive process, using pliable materials like plastic to print out an object layer by layer. The study’s authors recommend taking advantage of 3D printing’s unique capabilities to rethink the structures that are made with cement and find ways to make the material itself less resource-intensive.
“Through structural design optimization and functional hybridization in construction, cement-based construction 3D printing can be used to fabricate structures that use less cementitious materials, decrease the need for formwork and reduce waste, overall reducing emissions compared to conventional concrete construction,” said Del Gado, director of the Institute for Soft Matter Synthesis and Metrology.
The largest chunk of the process’s carbon emissions — accounting for more than 50% — comes from firing powdered limestone in a rotating kiln to form clinker, the building block of cement. Cement-based construction 3D printing (C3DP) has the opportunity to use lower-footprint mixtures that contain filler materials like industrial waste products and soil-based additives. Construction manufacturers need to be encouraged to develop greener cement mixtures for C3DP, the paper’s authors argue. Simply relying on the increased usage of C3DP isn’t enough as more carbon-intensive mixtures can be used.
Prioritizing Policy
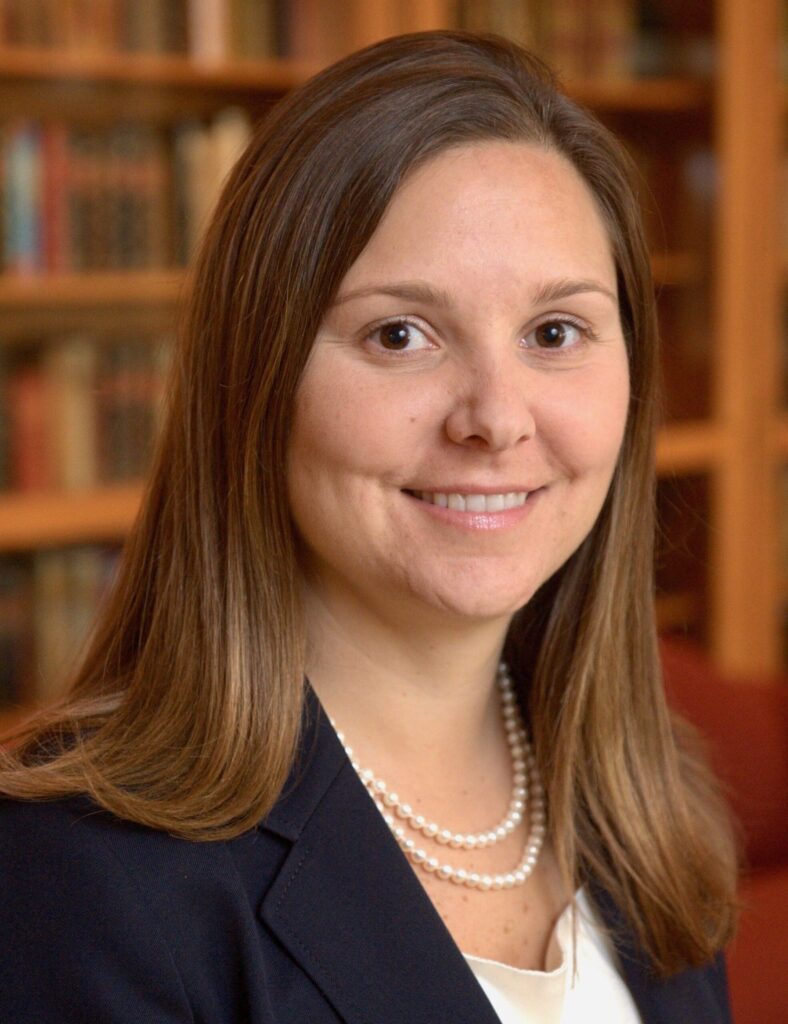
Joanna Lewis, director of the Science, Technology and International Affairs Program in the Walsh School of Foreign Service.
Already, stakeholders in both the private and public sector are interested in 3D printing. The U.S. Department of Defense is advocating for incorporating 3D printing in concrete construction and Dubai plans to use 3D printing in a quarter of all new construction by 2030. These plans, however, do not explicitly integrate carbon reduction.
“It is crucial for policymakers to recognize that unless programs and projects to demonstrate C3DP are designed with climate change in mind, the technology could end up incentivizing printable cementitious mixtures with higher as opposed to lower carbon footprints,” said Lewis, who is also director of the Science, Technology and International Affairs Program in the Walsh School of Foreign Service.
To guide C3DP towards reduced carbon output, Del Gado and Lewis propose a five-step action plan centered around researching printable low-carbon cementitious mixtures, freely sharing that research and encouraging public-private partnerships to prioritize low-carbon development.
Lewis and Del Gado note that this paper came out of a new interdisciplinary collaboration funded in part by an Earth Commons “ECo Impact Award” and led by their shared postdoctoral fellow, Ankita Gangotra, which allowed Del Gado, a physicist, and Lewis, a climate policy expert, to examine this technology which has important implications for the construction industry and for national competitiveness in advanced manufacturing.
by Hayden Frye (C’17)